Australian researchers develop intelligent 'Ladybird' farm robot
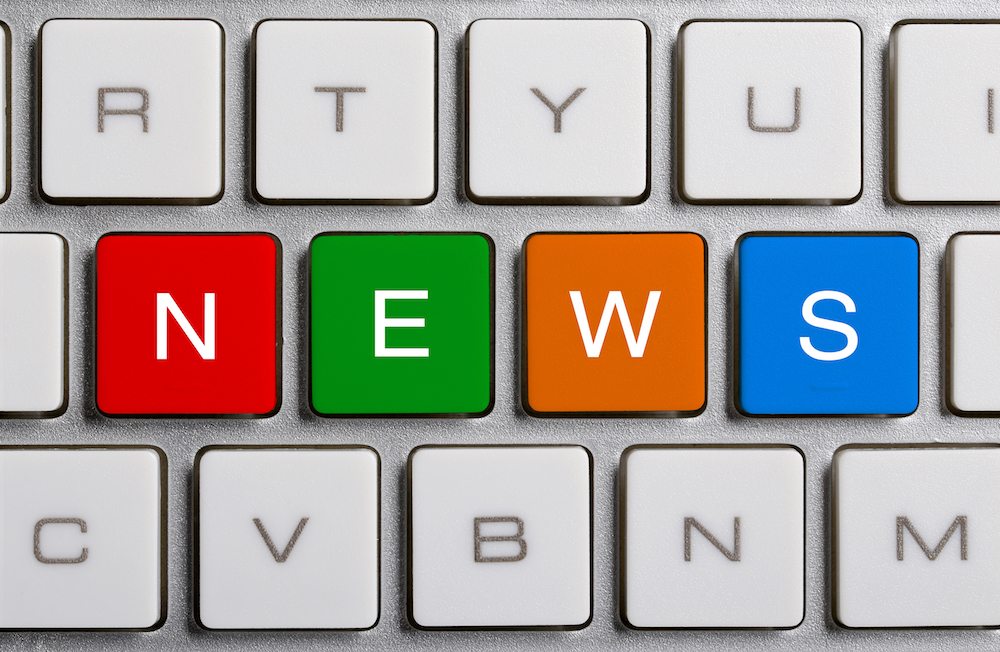
Researchers from the University of Sydney have developed a prototype robot that aims to advance agriculture robotics technology and provide new and important information to growers.
The robot, dubbed 'Ladybird' due its spotty red and black appearance, comes from a collaboration with Horticulture Australia Limited (HAL) and Ausveg, and is capable of driving around the farm and conducting autonomous tasks.Â
Research fellow at the university's Australian Centre for Field Robotics (ACFR) Dr. James Underwood told www.freshfruitportal.com a big advantage of the robot was the fact it did not just observe the crops, but could also take action when needed.
"We have a combination of different sensors on the new Ladybird robot platform – different cameras lasers and so on to map the color and also the 3D shape of the entire farm really down to the resolution of every individual leaf," Underwood said.
"Then in addition to that we have a robot manipulator arm on the platform so we're not just limited to sensing information passively but we can actually start to take action on the farm which could include things like contact sensing soil probes, and sensors that need to come into contact with specific vegetables."
The arm could also remove weeds from the field after having differentiated between them and the crops, and could even be used in the future to perform autonomous harvesting.
Another of the Ladybird's biggest advantages is its ability to provide farmers with key data about plant malnutrition, before a farmer would have normally realized there was an issue to be addressed.
"Nitrate deficiency can be detected by growers using their own eyes because when it occurs it causes the leave of spinach, for example, to turn yellow," Underwood said.
"But once that's occurred to the extent that it's detectable by the human eye it's essentially already too late – that particular crop can't be sold and it can't be fixed for that crop.
"If it were possible to use a senor to pick up on the subtle color changes a couple weeks earlier then that would be a significant benefit because that would be early enough for the farmers to address the nitrate deficiency problem with fertigation."
He added that often when farmers see a crop has turned yellow, while it is too late for that one they will often apply the corrective measures to surrounding crops in their field on the assumption that the same problem exists for all of them, which can be expensive if there is in fact no problem.
The sensors on the robot include lasers, cameras, and hyper spectra cameras, and has successfully completed tests at an Australian farm in Cowra.Â
It has been in development for around a year with a total cost of about AUD$1 million (US$944,000).
Underwood explained that due to the high cost it would be far too expensive to be economically viable as it is, but the team essentially wanted to test out all the sensors on this one prototype as a basis for further research.
"One of the purposes of the research that we're conducting here is we've built this robot that has more sensors that we think are probably likely to be necessary in the final solution, and part of our job as researchers is to figure out what is the lowest common denominator," he said.
"'How cheaply can we actually detect the things we need to detect in the field? Which combination of sensors is sufficient such that as a next stage commercial prototype we could put it together much more cheaply and cost effectively?'"
The researchers are also interested in systems research, and don't necessarily see the solution as being one single vehicle, but rather the most cost effective solution may end up as a combination of different types of platforms.
"For example, a small unmanned aircraft vehicle like a small helicopter or lightweight aircraft could fly around and survey from a relatively low altitude and could automatically feed that data back to other agents within this system," Underwood said.
"So having done a survey, a plane could send back the results of that survey and send a ground vehicle, perhaps, to a couple of specific regions of interest.
"As a result, that ground vehicle may be cheaper if the vehicle had to cover the entire farm every day"
An important part of the research is to figure out where that 'optimal point' lay in terms of system configuration.
"At the end of the day it’s about getting the right sensor to the right position in the field at the right time, and then having the algorhythms and the software and the math behind it that can process that data into original information for farmers to actually make use of," he said.
Underwood also said he thought it more likely that in the short-term agriculture technology startup companies would buy these robots and sell their services to farmers, rather than the farmers owning the robots themselves.
"I think in the longer term that's feasible having the farmer having it in the shed and the robot just does its thing. But I think in the shorter term it's much more likely that it will be that other model where a secondary company operates it," he said.
Along with the Ladybird, ACFR also has a variety of other robotic systems including hovering platforms that are equipped with cameras and able to fly very close to the ground, and an unmanned ariel vehicle called the J3 Club.
Related story: Australian researchers branch out with robot farming
Photos: Australian Centre for Field Robotics