UNITEC is close to its customers in the world, today more than ever
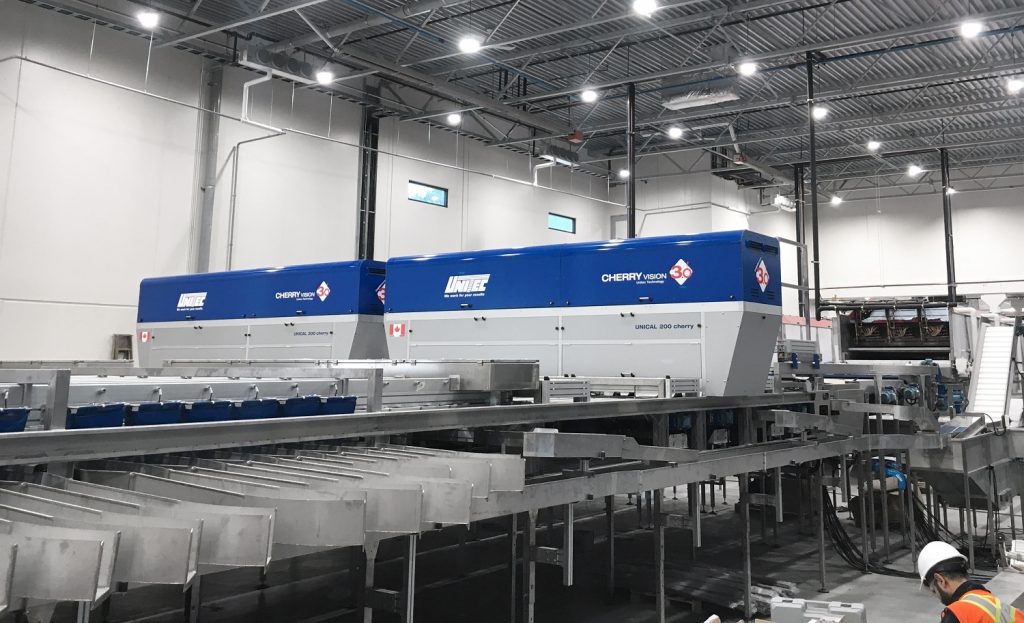
PRESS RELEASE
We have 100% experienced that, during this storm, UNITEC became our lighthouse.
Even during the lockdown in Italy, UNITEC together with Alanar Team has succeeded to load 10 trucks of equipment and send them to Turkey by sea.
Also, the installation team of UNITEC in Turkey has been working enormously - while keeping the safety distances in the facility and taking all necessary precautions - and at the same time has performed every day with its soul and full commitment to the installation.
We are about the see the light at the end of tunnel and the completion of Turkey’s very first line equipped with Cherry Vision 3.0, which will start on May 12 before the Cherry season and the exports from Turkey begin.
A lighthouse in the storm for its Customers. The metaphor of Emrah Ince, General Manager of the Tekfen Agri Group of which the Turkish packing house Alanar is part, has given a great joy to the UNITEC Team, which works for the Results of its Customers. Actually, it lives on these Results.
We work for your Results has never been just a slogan: the benefits and advantages that UNITEC technologies give to its Customers in the world are what the Company has worked for over 95 years, they are what repays it for its commitment and effort, day after day.
Needless to say, when the emergency situation due to the pandemic got worse, UNITEC first thought was to continue to ensure all the necessary support to its Customers, the Packing Houses all over the world which handle fresh fruits and vegetables, so that they could continue their activity in the best conditions.
UNITEC immediately mobilize with the aim of being able to ensure all the necessary assistance to its Customers, wherever they were located.
Thanks to the widespread presence of its 13 branches, to its teams of specialized technicians located in all continents and its after-sales service Team, UNITEC was able to meet the needs of its Customers, thus ensuring the complete functionality and efficiency of their lines.
However, UNITEC did not limit itself to provide assistance: in the middle of this emergency phase, it was able to continue – or even to start – the installation of new lines at the premises of many Customers.
This is the case of Turkish Customer Alanar, but also that of the Canadian packing house Jealous Fruit, specialized in producing and handling cherries in the British Columbia region:
We are now in the final stages of installing a 28-lane line, equipped with Cherry Vision 3.0 technology, in our new Kelowna facility.
This line has many innovations, including AC 350 automatic box fillers and the first automatic palletizers in North America.
We continue to be impressed with UNITEC professional customer driven approach, and the design and workmanship of their product.
More importantly, even in these difficult times of a worldwide pandemic, the project is ahead of schedule
and there has been absolutely no reduction in the UNITEC service standard.
This is how David Geen, President of Jealous Fruits, pointed out how UNITEC was able to move forward with the installation of a 28-lane cherry line with the Cherry Vision 3.0 technology, despite the difficulties of this period.
The packing house from British Columbia was not the only one in the American continent that, during this period, benefited from UNITEC support in the extremely delicate stage of installation of a new line.
Chris Carloni, Director of Operation of the Californian packing house OG Packing, expressed all his gratitude towards UNITEC, which despite the restrictions cause by the emergency situation was able to update the Cherry Vision 3.0 system in three cherry sorting lines in the Stockton installation, thus respecting all the commitments made with the Customer:
In this very difficult and uncertain time, we are grateful to have a business partner that has supported us and our needs above and beyond our expectations.
UNITEC has rapidly restructured their technical teams to fulfill its commitments to OG Packing and adapt to the travel restrictions and mitigation efforts currently in place due to the Covid-19 pandemic.
Cherry Vision 3.0 system represents a technological performance evolution of the Cherry Vision 2 system that the Customer previously had. It is an intelligent automated technology, which allows a greater precision and reliability in classifying the external and internal quality of cherries. At the same time, it allows to minimize/eliminate the personnel necessary to carry out the selection.
UNITEC lines, thanks to their high level of automation, allow packing houses to minimize the labor on the lines, thus allowing the operators to work in compliance with the safety distances.
And the added value of automation doesn’t end here, it becomes a true safety guarantee for the consumer. UNITEC lines allow fruit and vegetables to come into contact with operators as little as possible during the different stages of the handling process, from the moment the product enters the packing houses to the final packing before shipment to the point of sale. This way, the risk of contamination by personnel is avoided.
UNITEC support in the delicate stage of the installation of a new line arrived all the way to Oceania. Here re the words of Helen Aggeletos, General Manager of Australian packing house Venus Citrus, where UNITEC was able to complete the installation of a new line for handling mandarins equipped with the Mandarin Vision 3 technology.
Exciting times for Venus Citrus with the completion of the new installation of our UNITEC line.
It has been a challenging six weeks due to the restrictions of the Covid-19 virus, a continuing moving target due to travel restrictions.
UNITEC was able to organize a team of qualified technicians on the premises in order to meet deadlines as the Italian team could not travel to Australia.
The technical team was amazing committed to meeting deadlines and completing the installation, working around the clock to get the line up and running in time or our upcoming Citrus season.
The same satisfaction and gratitude of our overseas Customers was also shown by European Customers, such as our Spanish Customer Rio Cinca.
Oscar Ortiz, General Manager of the Spanish packing house Rio Cinca, commented on the upgrade of his cherry line to UNITEC Cherry Vision 3.0 technology and the approach to the installation of the new processing line for peaches and nectarines equipped with the Peach Vision 3 system, at his premises in Torrente de Cinca. With as much conciseness as clarity, he stated:
We express our gratitude to UNITEC for meeting all deadlines so far, despite the difficult situation we are in.
“Meet all deadlines”: these simple words were repeated from mouth to mouth, from one Customer to another. It is not an easy thing to do when you are in the middle of a pandemic that affects everyone's lives. However, it is a common and essential goal.
“We have believed and invested over the years in building a network of operating branches in the countries with the highest fruit and vegetable vocation of all continents, so as to guarantee a prompt intervention and meet the needs of Customers all over the World,” said Angelo Benedetti, President of UNITEC.
“All of this must be done in line with the company philosophy of being close to our Customers all over the world. Wherever they are. Let’s build together successful results. For them, for their fruit.”