Robotic pruner ready to cut down production problems in apple orchards
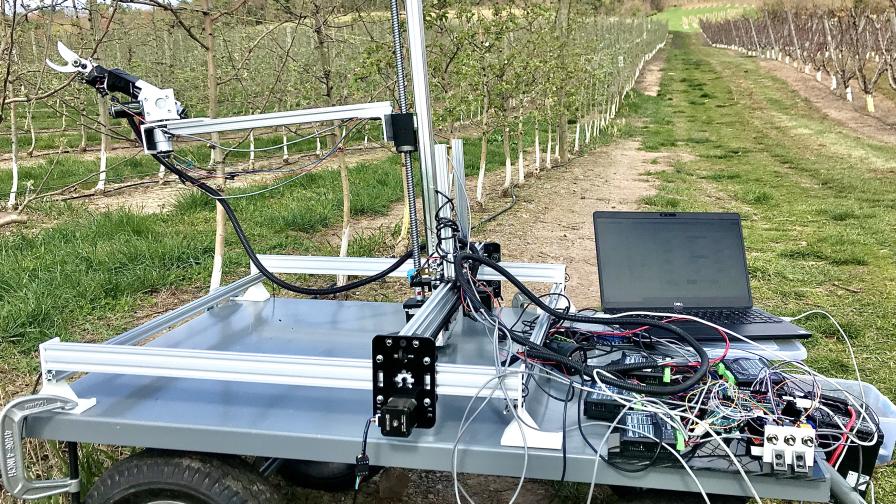
The content of this article 'Robotic pruner ready to cut down production problems in apple orchards' was prepared by Thomas Skernivitz and has been revised and republished by FreshFruitPortal.com.
While the whole of agriculture trends toward automation technologies, the production operations of tree fruit crops still require a fair amount of manual labor.
The pruning of apple trees, for instance, comprises about 20% of total preharvest production costs. Between 30 and 35 working hours of skilled labor are required per acre for manual pruning of apple trees. The dilemma increases evermore as the labor force diminishes and labor costs rise.
“There is a need to find a potential solution to this problem,” Azlan Zahid, a graduate student at Penn State University, says.
Zahid and his colleagues at Penn State have designed the first robotic mechanism — an end-effector cutter — for a fully automated, computerized pruning system for modern apple orchards.
To date, the concept of integrating such a Cartesian- and rotational joint-based robotic system has shown promising results while overcoming difficult pruning conditions, he says.
Apple Tree Obstacles
The complications that accompany the concept of robotic pruning are largely due to the unstructured working environment that an apple tree presents. The robotic cutting unit has to be able to operate in tight spaces and reach targeted branches for pruning while avoiding the tangle of other branches.
“The branches grow in a random orientation and direction, which basically causes difficulty for the reconstruction of the branches and also for the maneuvering of the system within the tree canopy,” Zahid says.
A second challenge involves the spatial requirements of the maneuvering system. “Because of the complex tree architecture, there is very little space available within the tree canopy in which the robot can actually move and perform the operation,” Zahid says.
Motion Offense
Zahid and his team (Md Sultan Mahmud, Long He, Dana Choi, Paul Heinemann, and James Schupp) set out to develop a six degrees of freedom (DoF) pruning manipulator that meets maneuvering, spatial, mechanical, and horticultural requirements.
It is comprised of two parts: a wrist end-effector – the cutter – that boasts three rotations (yaw, pitch, and roll); and a three-directional linear manipulator built to house the end-effector and move it to the targeted pruning locations.
To provide information for the end-effector design, the researchers measured branch-cutting force with a sensor attached to manual pruners. The piece was then developed using three rotary motors and a pair of shear-blade pruning cutters powered with a geared electric (DC) motor.
To guide the maneuvering of the end-effector and the manipulator control, they developed an embedded microcontroller system with a user interface, using an interactive mathematical program that allows calculations to be visualized.
A mathematical model was developed for simulation of workspace utilization, kinematic dexterity, and reachable points for the end-effector.
The apple tree was reconstructed using the three-dimensional (3D) point cloud data by segmenting the tree trunk and the primary branches. Multiple computer algorithms generate collision-free robot trajectories and find a smooth and optimized path to reach the targeted pruning locations.
Field Studies
The researchers assessed the performance of the prototype during field studies at Penn State’s Fruit Research and Extension Center in Adams County, PA. Ten ‘Fuji ’/Bud.9 trees were selected randomly from a trellis fruiting wall. Eight to 10 branches were selected from each tree.
The average time to reach the target branch was about 12 to 13 seconds. The robotic pruner successfully cut branches up to approximately 25 millimeters (mm) in diameter, which, Zahid says, is “well above the range of the usual branch diameter with the modern tree architecture system.”
“We were able to cut and reach all of the branches we have in the trees,” he says. “And the path-planning algorithms we developed were successful in generating collision-free paths for reaching the targeted pruning points.”
Machine Vision Needed
There is room for improvement, Zahid notes. His team will add multiple approaching angles to the system, as it is not possible for the cutter to reach perpendicular to the limb orientation every time due to the complex tree canopy, he says.
“We have added multiple reaching options for the robot (approaching poses) in the computer program for this, which basically improves the ability of the system to find the collision-free path reaching the target branches,” Zahid says.
However, adding a large number of reaching options may result in increased time of operation as the robot searches the path for next or alternate approach option after the current approach fails, he says.
This can be optimized, he adds, by using advanced computation techniques, such as parallel computing. By doing this, the robot can search the path for all approaches simultaneously and then can select the optimum path automatically.
“As we used a LiDAR (light detection and ranging) sensor for 3D reconstruction of apple trees, some small/thin branches were missed by the LiDAR sensor due to resolution limitation.
Also, the branch diameter could not be measured accurately, thus necessary to accomplish this will be an efficient machine vision system, such as using a RGB-Depth (RGB-D) camera vision system to accurately measure the branch diameter to automatically make the pruning decisions, as branch diameter is one of the most important parameters for pruning branch selection,” Zahid says.
The development of pruning cut sequencing algorithm is also essential to optimize the path lengths and cycle time for efficient robotic pruning operation, he says.
“We need to integrate a pruning cut sequencing algorithm, so we know which branch we need to cut first and which branch we need to cut second,” Zahid says. “We’ll basically integrate these two systems to develop a complete robotic pruning system.”