OPS: Lasering weeds and other developments
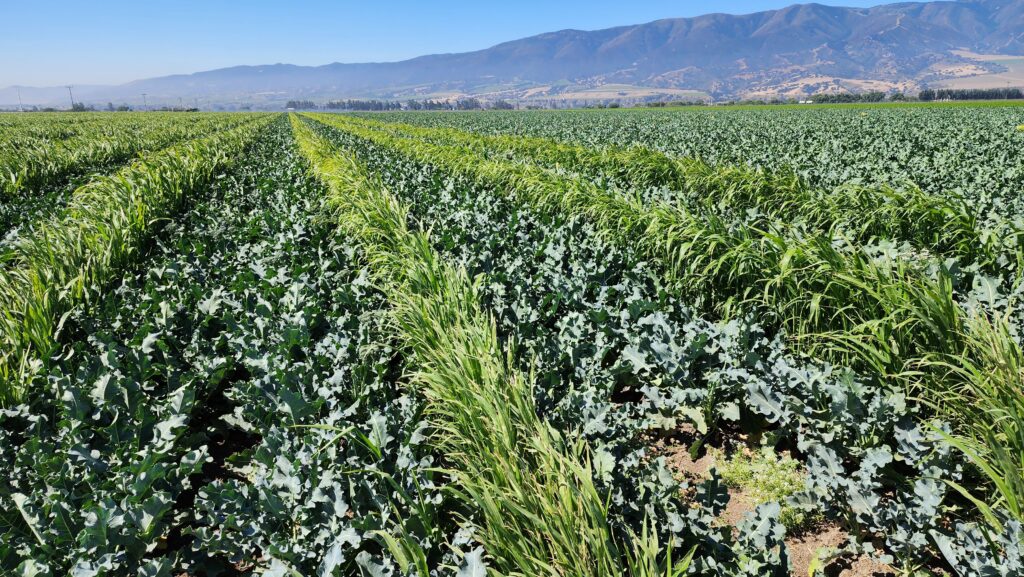
The Organic Produce Summit (OPS) shot to a strong start on July 12 in Monterey, CA. Matt Seeley, founder of the show, tells FreshFruitPortal.com this is the seventh OPS. The 2020 show was canceled for the Covid pandemic, or this would have been the eighth meeting. He indicates he is very happy about the attendance and organization of the 2023 show.
Related articles: OPS keynote addresses 63 million tons of food waste
While attendees, arriving from around the country, flew through a thick, chilly fog bank the previous day, Wednesday’s sun burned off the fog to present a splendid opening day clear warm sky.
Sunny weather was great for the opening-morning Salinas Valley tours, which went to Braga Farms, Driscoll’s, or Earthbound Farms.
FreshFruitPortal.com happened to catch a full tour bus to Soledad, CA, where Braga Fresh Family Farms grows 5,000 acres of vegetables. A well-organized tour split participants into four groups to personalize and maximize effectiveness. A number of articulate, informed professionals described various aspects of Braga operation. They looked sharp in matching polo shirts, bearing the company logo.
Organic production currently totals 40% of Braga’s vegetable output.
The grower is thoughtfully and cautiously studying, developing and testing new methods to build sustainable production. With careful production techniques, Braga is getting as many as 3.5 crops per year on some of its acreage.
Two per year is more common in this valley. Braga is a medium-sized grower by local standards, and its size is sufficient to apply some practices not available to smaller growers, but its moderate size makes it more flexible than Salinas’ industry vegetable giants.
One third of Braga’s fields are fallow at all times.
Eric Morgan, Braga’s vice president, environmental science, and resources, explains that his production focus has shifted to prioritize healthy soils over first thinking of healthy plants. Starting with healthy soil brings healthy plants. And healthy plants are resistant to insects, who prefer feeding on weak and dying plant life.
Morgan stood before a successful demonstration plot of sweet baby broccoli. Between the broccoli rows were tall rows of rye grass. He explained that rye roots grow deep into the soil, and hold moisture there, while offering other complex biological benefits. (Even after the rye is cut when the crop is harvested, the grass roots remain deeply in place and continue to benefit the soil composition.)
Beside this plot was a sweet baby broccoli planting without the rye. To the layman’s eye, the broccoli plots looked the same, but Morgan said the rye added to the quality of the broccoli.
With the attention to healthy soils, Braga is putting a great emphasis on reducing the tillage of its fields. One of the benefits is that deep tilling – which can go as deep as three feet, releases value CO2 into the atmosphere. Braga is bringing expensive shallow-till plows into use, which go just inches into the dirt. This minimizes CO2 loss into the atmosphere. Furthermore, the huge field tractors use much less diesel fuel and emit less pollution.
Morgan emphasizes that this tilling work is in its early stages, and he hesitates to make great claims about benefits, but the outlook is very promising, as the work moves ahead.
Braga featured a couple highly sophisticated AI pieces of field machinery. One blasts weeds with lasers. The other mechanically harvests broccoli. In both cases, workers doing tedious, backbreaking field work can be released to more pleasant tasks.
The weed blaster is on a trailer, armed with three rectangular boxes holding three laser lights on each side of the machine. Computer eyes identify weeds and direct the light to laser the weeds, which literally go up in a puff of smoke when they’re burned.
The AI broccoli harvester is one of six Braga has on hand. These were designed and built by Automated Harvesting Solutions, LLC, in Burlington, WA. Karl Thomas of Automated Harvesting told FreshFruitPortal.com that each new machine is tweaked with improvements. But computer eyes are trained to size up broccoli heads as the tall machine rolls down rows. Sophisticated cutting equipment eyes each stalk and cuts it in a commercially desirable fashion.
Thomas notes the machine doesn’t need to work by day, as its cameras are fully functional in the dark. So, harvesting no longer needs to be limited to sunlight.
The OPS crowd was allowed to sit in the control seat of the broccoli harvester. The controls looked like something that would be familiar to – and comfortable for operation – by any 14-year-old American kid.
Braga has been developing sweet baby broccoli sales since the items came to the United States in 1998. The OPS tour included a look at a new, efficient, field harvester for the commodity.
What this means
These Salinas Valley organic growers of sustainable vegetables are not your forebearers’ organic, bug-picking dreamers.
OPS is a great place to come to understand all the technical aspects of production. And learn what the industry can one day become. The July 13 seminars will have speakers discuss a variety of related, evolving topics, as well as an afternoon trade show.